Lean Manufacturing Consultants
Lean Manufacturing Consultancy
Our Lean experts will teach you everything you need to know about Lean tools and methods. You’ll learn how to cut out unnecessary steps, reduce waste, save money, and better achieve your business goals.
Our experienced team has the practical skills to help your company improve quality and meet the changing needs of your customers.
Learning these skills will give your business a major boost. Our expert trainers won’t just explain the theory, but will also equip your team with the skills to take concrete steps toward improving your production process for the best possible results.
Ready to start your journey?
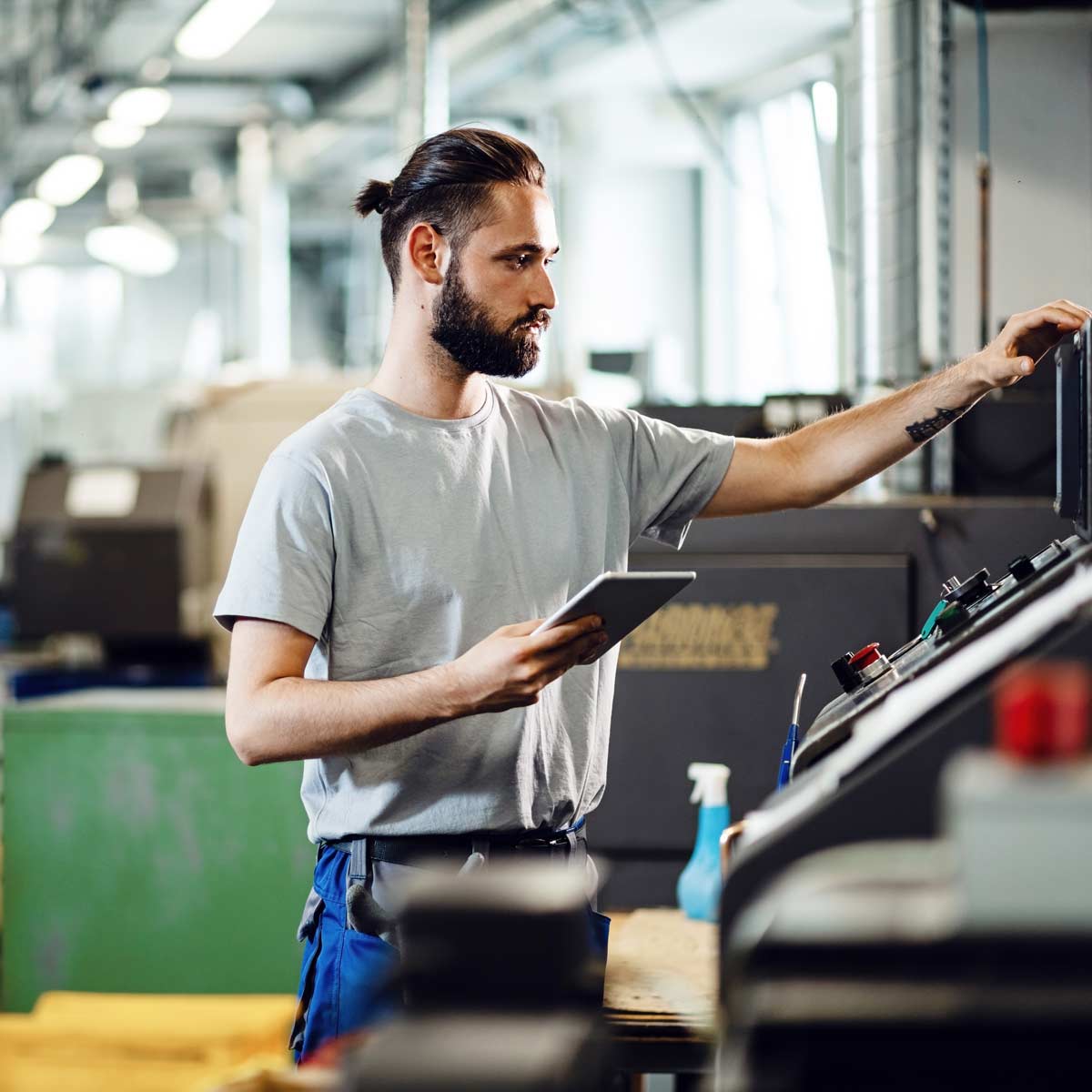
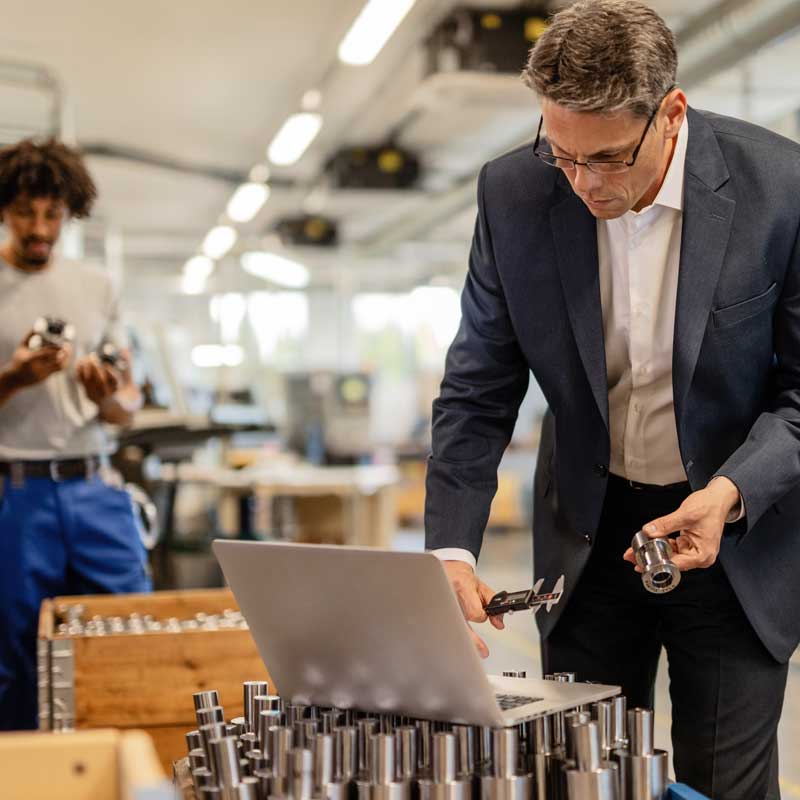
What Do Lean Manufacturing Consultants Do?
They help spot and fix waste that happens when demand changes. Sometimes customer needs shift, or the company adds new production lines, which means extra work.
Other times, waste comes from doing more than needed, requiring time to move from old tasks to new ones. Some processes don’t add value at all, even though some activities do. A Lean Manufacturing consultant helps manage these processes to meet changes in demand, reduce unavoidable waste, and cut out unnecessary waste.
Lean Implementation – Areas of Focus
- Understanding Waste in all its forms – reducing non-value-adding activity.
- Process Mapping – ensure a clear understanding of how a process works and help identify improvement areas.
- Business Performance Measures – data collection & analysis.
- Failure Mode and Effects Analysis (FMEA)
- Approach to Improvements – Plan, Do, Check, Act (PDCA), Kaizen, DMAIC.
- 5S System of Workplace Organisation
- Root Cause Analysis – cause and effect.
- Kanban Pull System
- Standard Operating Procedures
- Runners, Repeaters & Strangers
- Factory floor layout optimisation – new or existing facilities
- Implementation of the above into production & processes.
How We Support You
Our experienced consultants work alongside your teams to deliver tailored Lean support that fits your goals and your pace.
Here’s how we help:
Process Mapping & Waste Identification
We map out your current processes and identify where time, materials, or effort are being wasted.
Workplace Organisation (5S)
We help your team create clean, organised, and efficient workspaces that make daily tasks simpler and quicker.
Standard Work Implementation
Together, we build easy-to-follow procedures to keep things consistent, safe, and productive.
Problem Solving & Continuous Improvement.
We train your people to spot issues early and fix them fast, so problems don’t keep repeating.
Leadership Engagement
Lean needs buy-in from the top. We work with your leadership team to support cultural change and set the right tone from day one.
Why Lean Works
Lean isn’t just about tools it’s about people.
When your team understands the “why” behind the changes, and feels involved in the process,
they’re more likely to stay engaged and help things stick.
That’s why our approach always puts your people at the heart of the journey.
Why Lean Matters Now More Than Ever
In the current competitive landscape, Lean Manufacturing offers a pathway to resilience and growth:
Adaptability: Lean methodologies enable businesses to respond swiftly to market changes,
ensuring sustained competitiveness.
Integration with Technology: The synergy between Lean principles and modern technologies, such as automation
and data analytics, enhances operational efficiency.
Sustainability: Lean’s emphasis on waste reduction aligns with environmental sustainability goals, making it a strategic
choice for forward-thinking manufacturers.
The Benefits of a Upskilling Your Team
with Lean Knowledge
– Smarter production processes
– Improved capacity and staff knowledge
– Reduced lead times
– Increased profits
– Professional advice from a BrookConsult expert trainer who will bring experience from industry and from supporting
other businesses implement Lean into their operation.
What our clients say
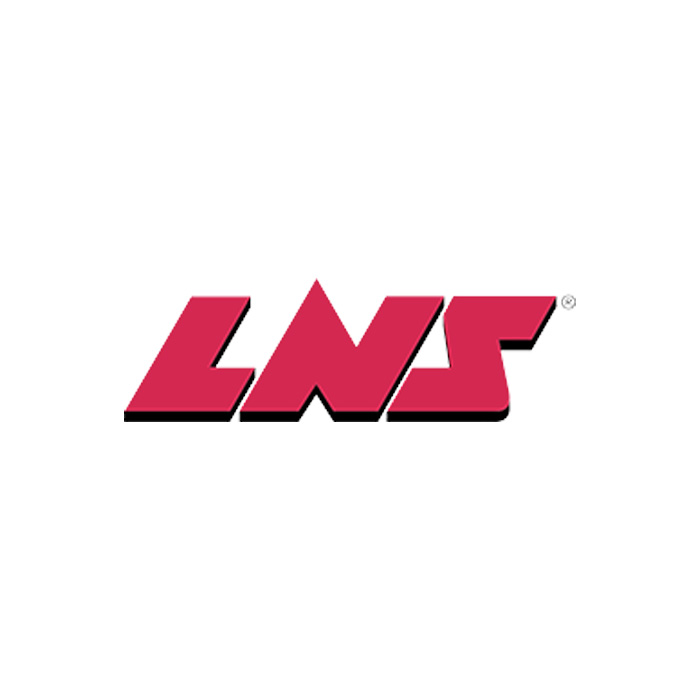
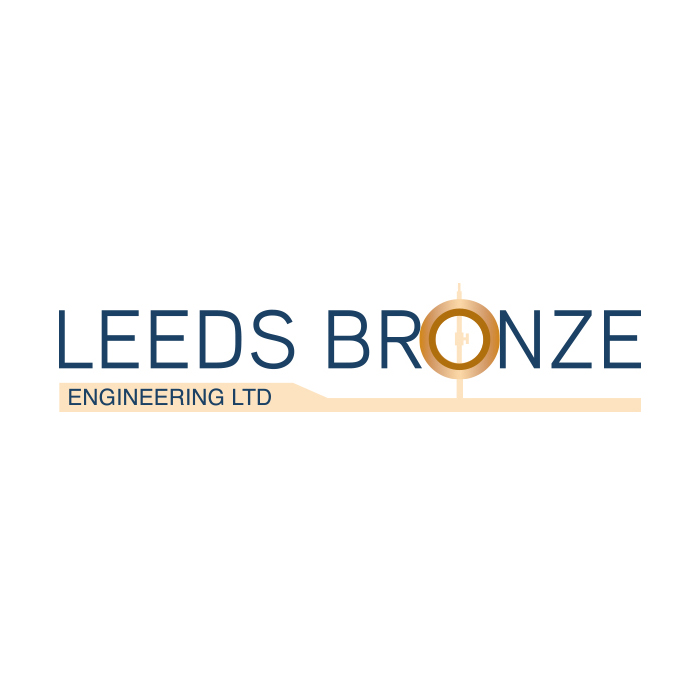
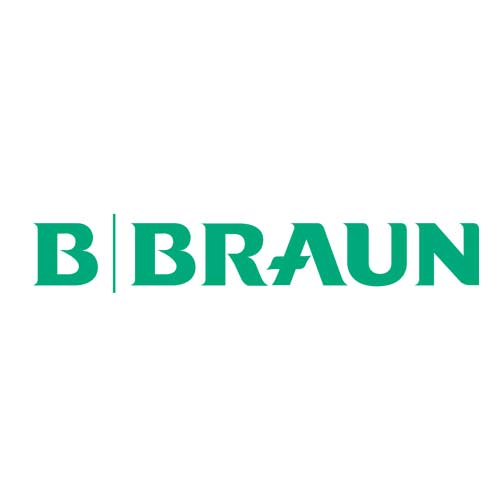
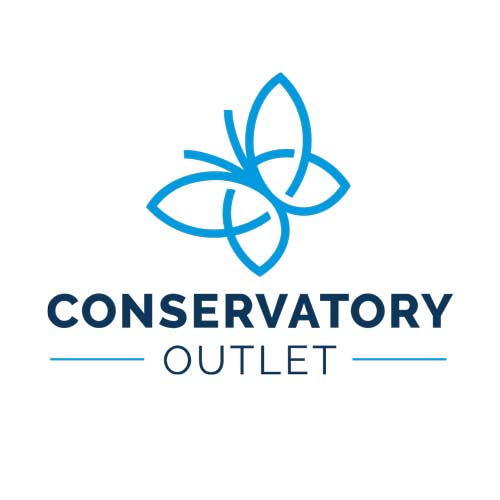
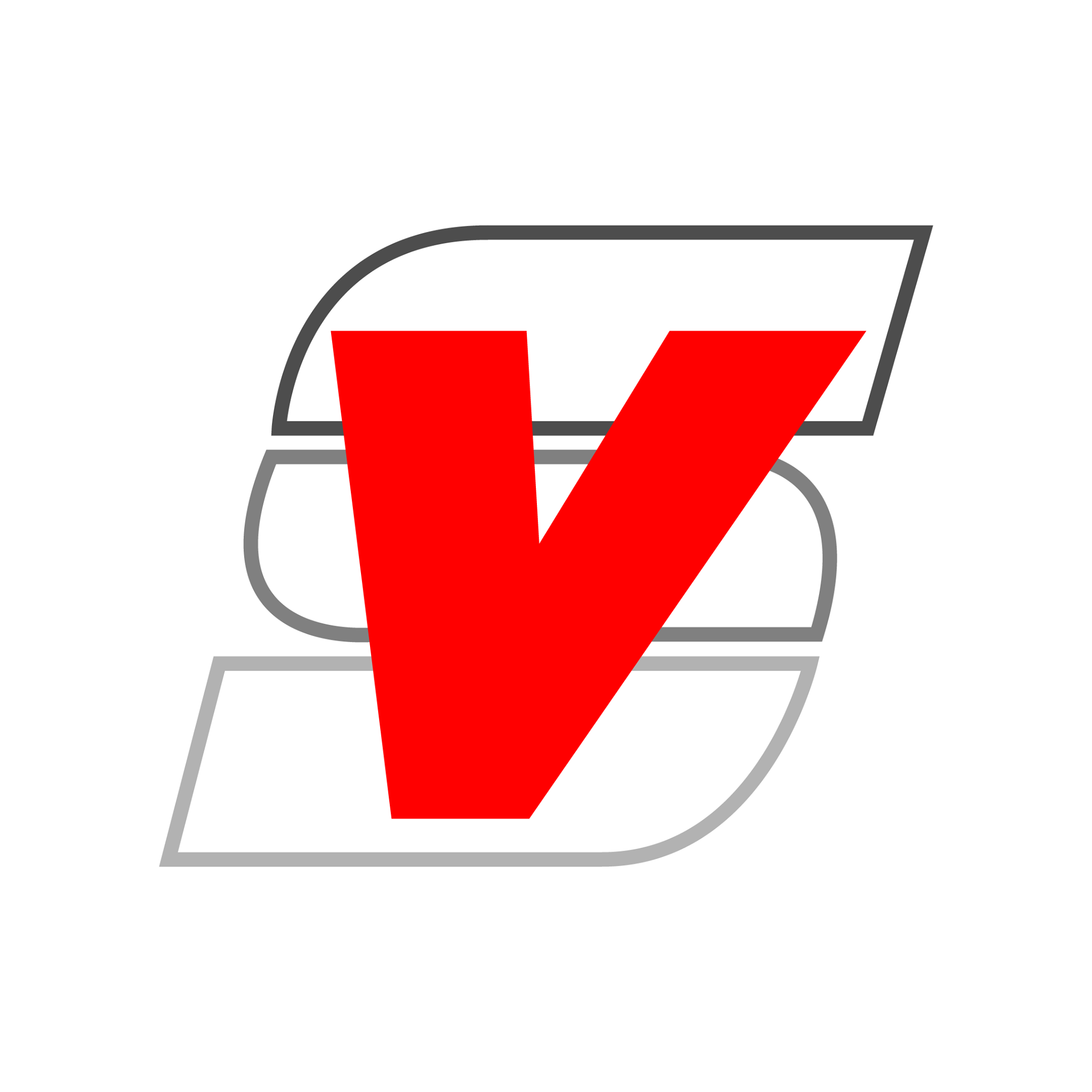
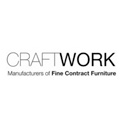
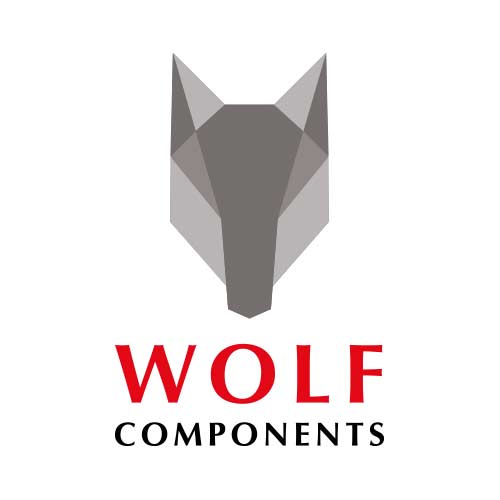
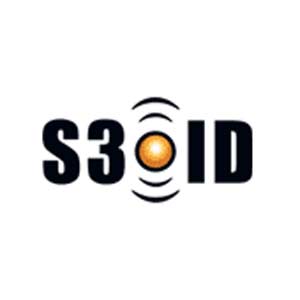
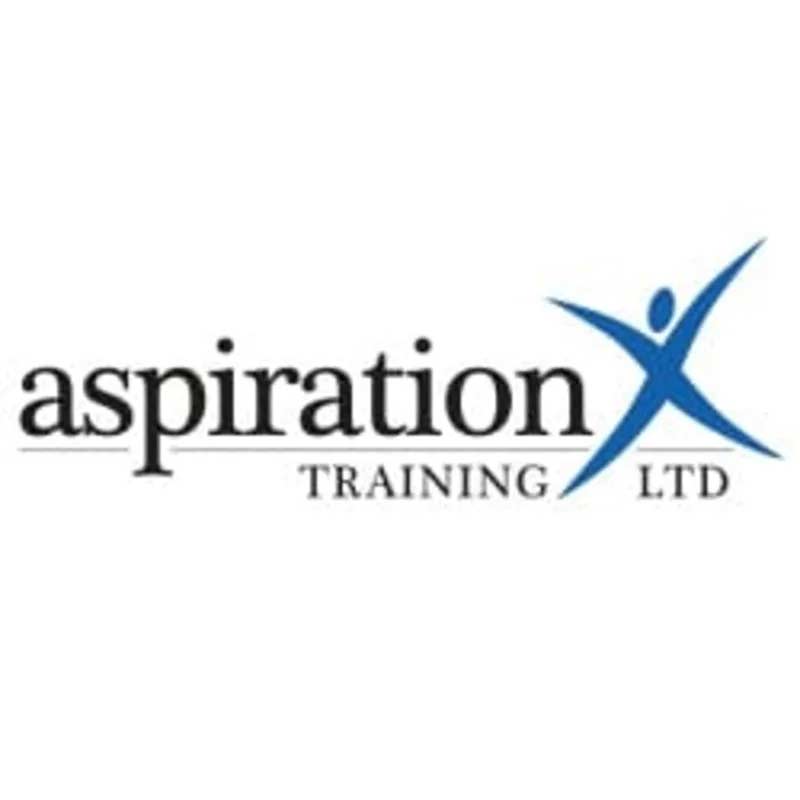
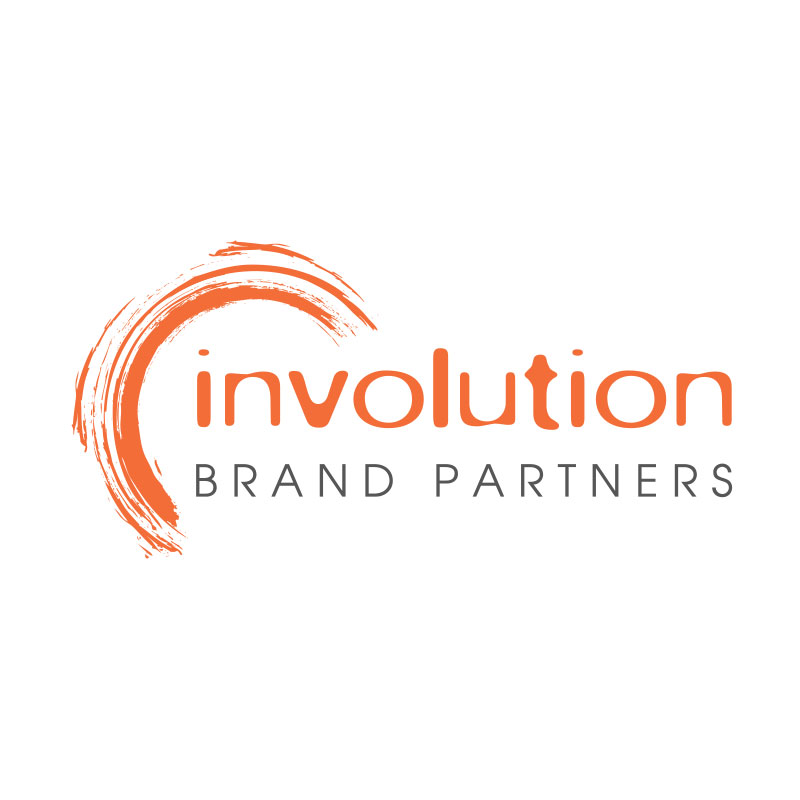
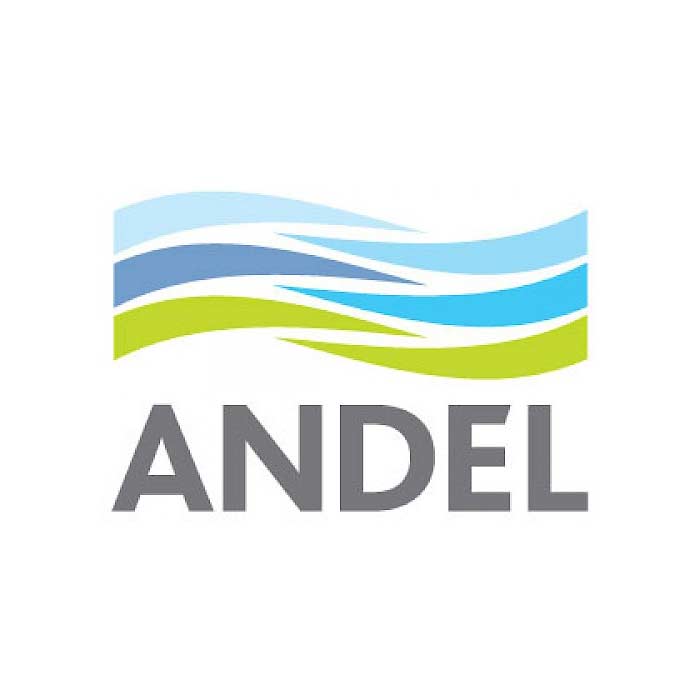
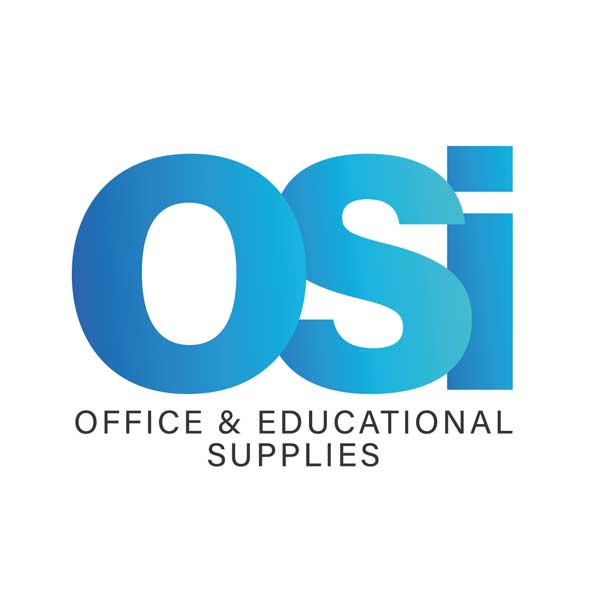
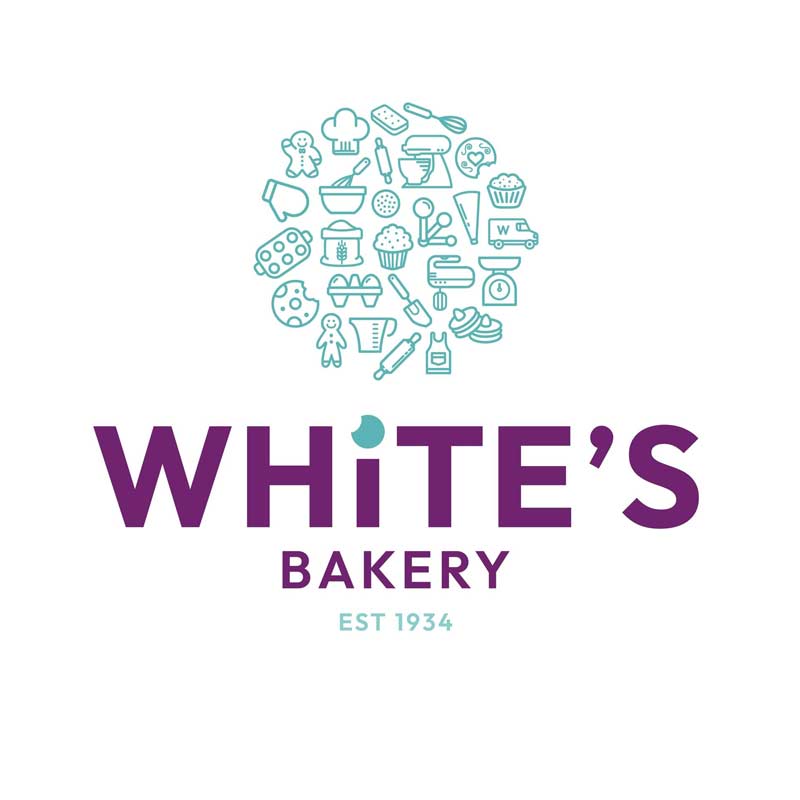
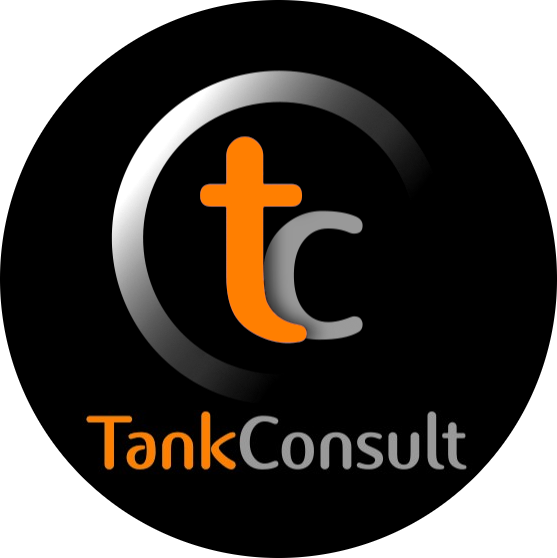
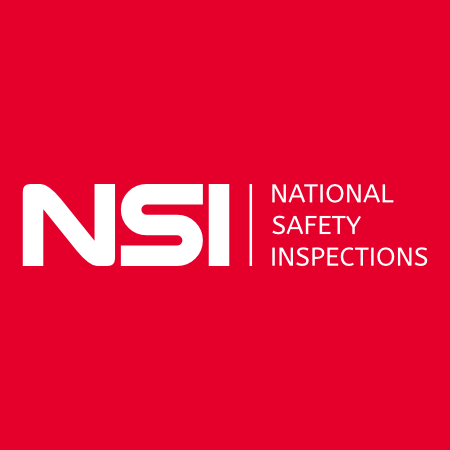
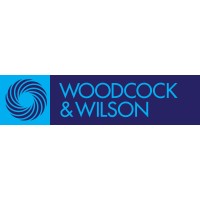
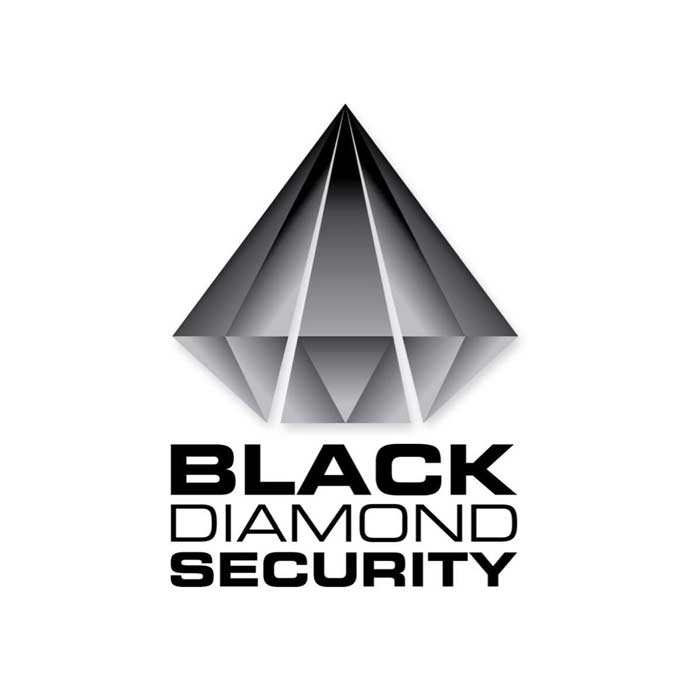
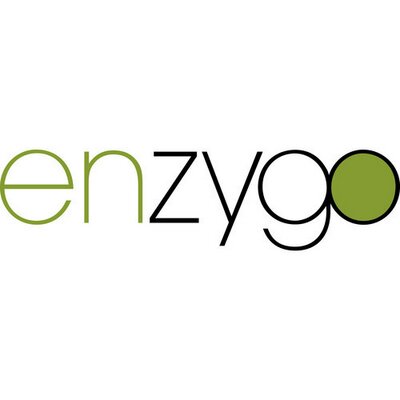