Six Sigma Certification
Six Sigma, Certification, Training & Consultancy
BrookConsult’s specialist trainers provide specialist Six Sigma training and consultancy for businesses that wish to maximise their full potential, identify new opportunities, and improve their operations.
Our team of Lean and Six Sigma experts have industry experience and knowledge to help your organisation improve quality and production standards to meet the ever-changing demands of your clients.
We are expert trainers, committed to helping you understand how the Six Sigma methodology can transform your operations.
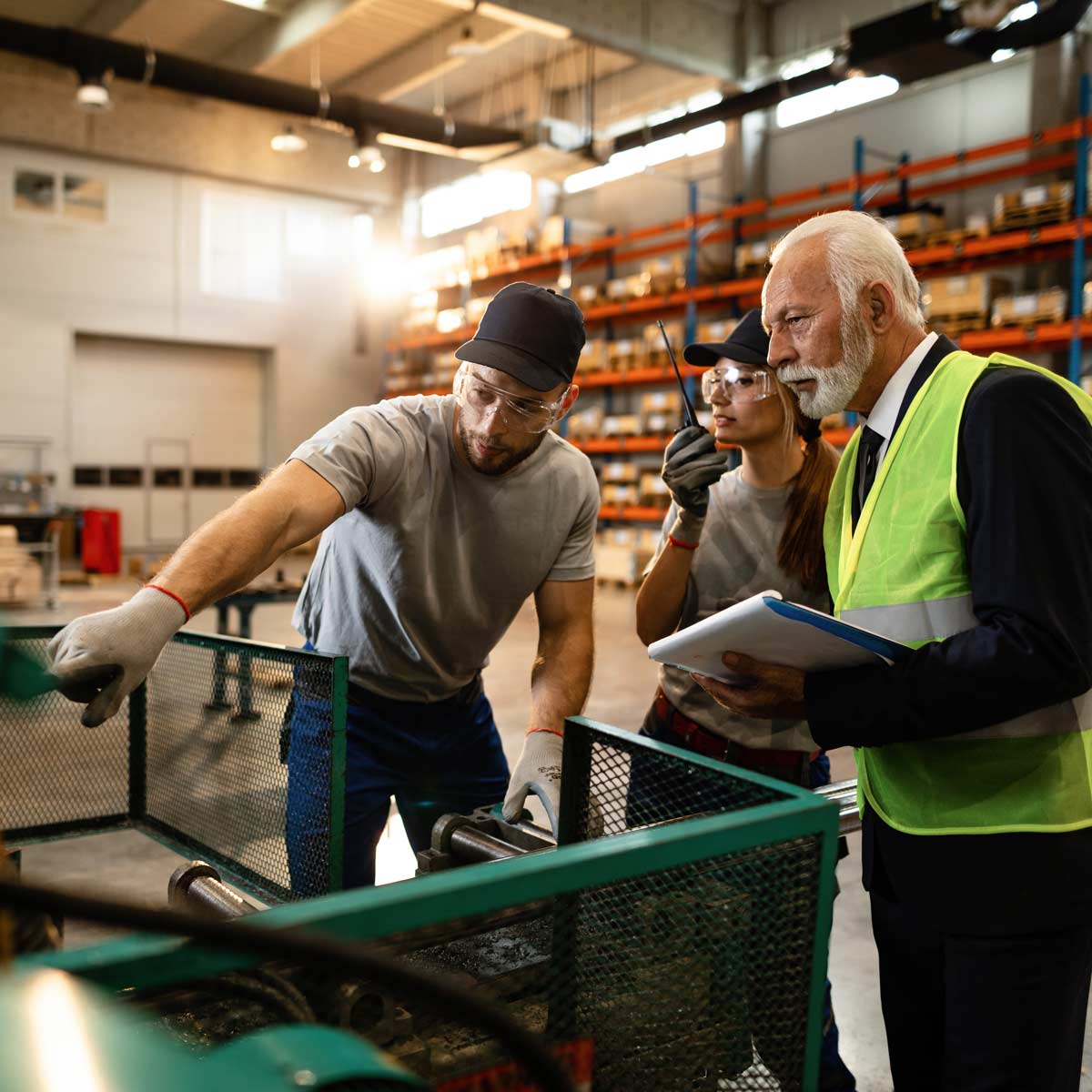
The Power of Six Sigma
Six Sigma is a powerful methodology and set of tools that focuses on improving processes by reducing variation and defects.
The “Power of Six Sigma” refers to its ability to drive transformative change and performance improvements across an organisation.
Six Sigma provides a structured, data-driven approach to identifying and quantifying performance gaps, analysing root causes, and implementing solutions to optimise processes and products.
It emphasises the power of people, process, and statistical analysis to achieve breakthrough results.
By leveraging Six Sigma techniques like DMAIC (Define, Measure, Analyse, Improve, Control), organisations can systematically enhance quality, increase efficiency, reduce costs, and ultimately deliver greater value to customers.
The power of Six Sigma lies in its rigorous problem-solving framework, which promotes a culture of continuous improvement and empowers employees to make data-backed decisions for sustainable change.
Its widespread adoption across industries is a testament to the transformative power of Six Sigma in driving operational excellence and business success.
Five Ways Six Sigma Can Transform Your Business
- Improved Quality: Reduces defects and variability in processes.
- Increased Efficiency: Streamlines operations to enhance productivity.
- Cost Reduction: Lowers operational costs by eliminating waste.
- Customer Satisfaction: Enhances customer satisfaction through consistent, high-quality output.
- Data-Driven Decisions: Utilises statistical analysis for informed decision-making.
The Five Principles of Lean Six Sigma
The five core principles of Six Sigma are all about creating a culture of continuous improvement and eliminating defects in processes. Here’s a breakdown of each principle:
1. Focus on the Customer: This principle emphasises that all improvements should be driven by meeting customer needs and expectations.
2. Measure and Analyse Everything: Six Sigma relies heavily on data and statistical analysis to understand processes, identify variations, and pinpoint root causes of problems.
3. Eliminate Variation and Waste: The core idea is to minimise any variations in a process that can lead to defects or inefficiencies. This involves streamlining processes and removing unnecessary steps that don’t add value.
4. Promote Teamwork and Communication: Effective Six Sigma implementation requires collaboration across teams. Clear communication is essential for everyone to understand goals, roles, and data.
5. Embrace Continuous Improvement: Six Sigma is not a one-time fix. It’s a philosophy that encourages ongoing process evaluation, improvement, and adaptation based on data and feedback.
Six Sigma certifications come in different levels, often referred to as “belts,” much like in martial arts, which indicate the holder’s proficiency:
Lean Six Sigma White Belt
Basic understanding of Six Sigma principles. Focuses on the overall process and how teams can use them to improve performance.
Lean Six Sigma Yellow Belt
The Lean Yellow Belt is the starter level qualification for Lean Six Sigma. This certification is tailored to individuals who want to increase their knowledge and understanding of Lean Six Sigma and seek to develop business performance. These applicants are usually employed in small, entry level roles and seek to improve their work rates and skills so that they can contribute to business success.
Six Sigma Belts do not have to be achieved in order, at any point an applicant can choose to train for a yellow, green, black or master black belt, where it corresponds with their role or plans for progression.
A Lean Six Sigma Yellow Belt can even be suitable for executive members looking to enhance their understanding of Six Sigma and improve their skills.
Lean Six Sigma Green Belt
Lean Six Sigma is a historically-proven methodology that aims to drive business profit through inspiring collaborative team effort and reducing waste. The tem ‘waste’ is used to represent elements that are outside of business necessities, for example practises and expenditures that can be deemed as over-processing, overproduction, defects and inventory.
There are four levels of Six Sigma belt classification – yellow, green, black and master black. The Six Sigma Green Belt is created for professionals who lead business improvement projects and already have a sound understanding of the core and advanced factors of Lean Six Sigma. This individual is likely to be under the leadership of a certified Black Belt.
During your training for the Six Sigma Green Belt Certification, you will be pushed towards achieving certified project manager status. Our Six Sigma trainers will provide you with all the information and tools you need to enhance your teamwork, leadership and management skills.
Once you’ve completed your Green Belt training, you will possess excellent team leadership skills and develop a firm understanding of all aspects of the Six Sigma methodology.
Lean Six Sigma Black Belt
Black Belts are advanced practitioners who lead Six Sigma projects and oversee Green Belts. They focus on project leadership, statistical analysis, and problem-solving.
Lean Six Sigma Master Black Belt
The highest level of certification. Master Black Belts mentor Black and Green Belts, strategise high-level initiatives, and focus on enterprise-wide implementation.
What our clients say
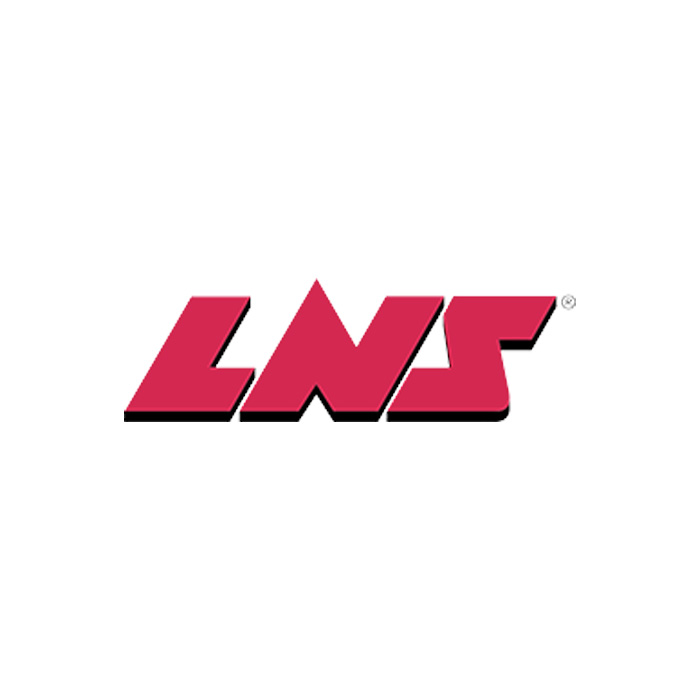
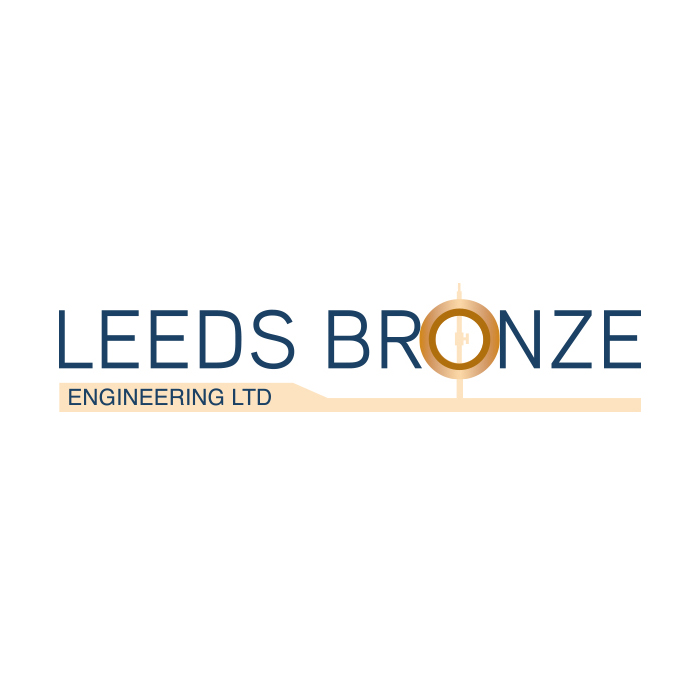
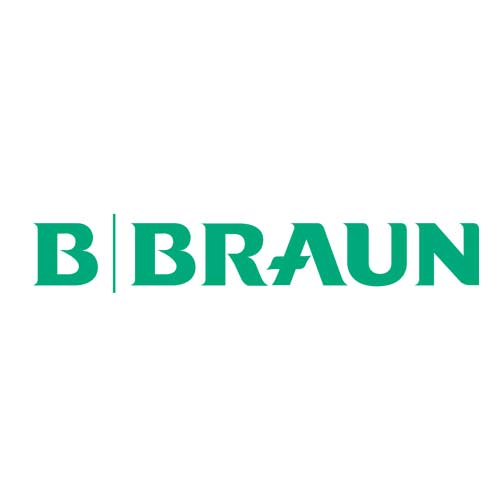
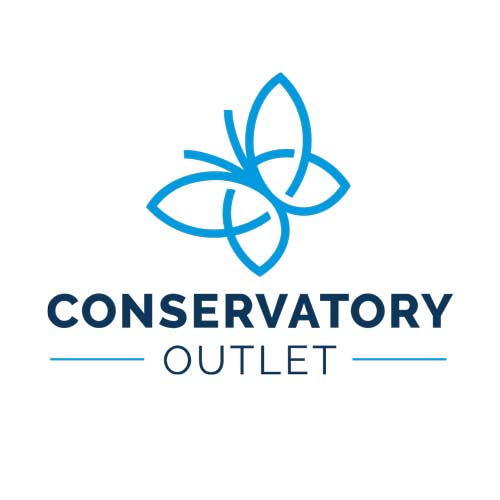
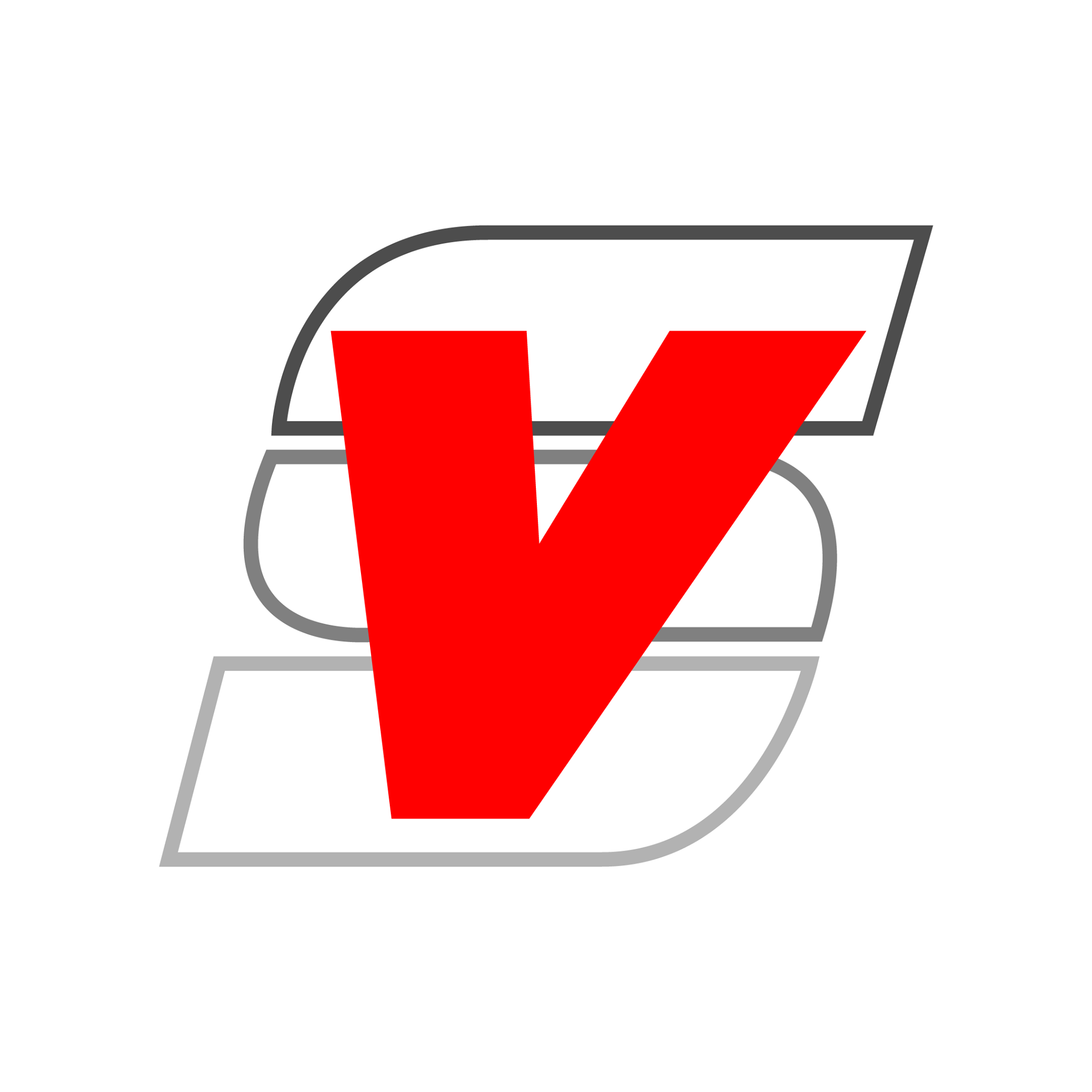
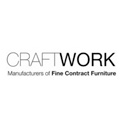
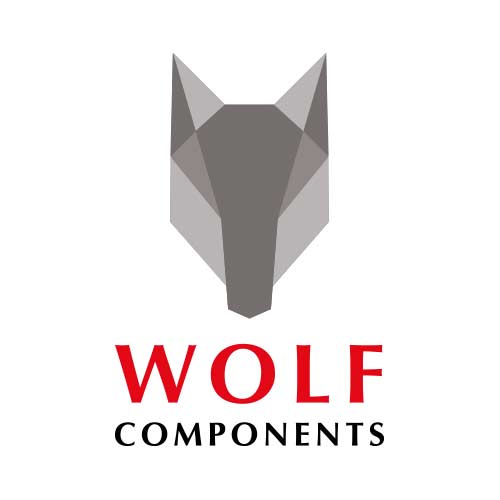
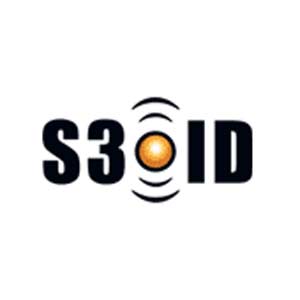
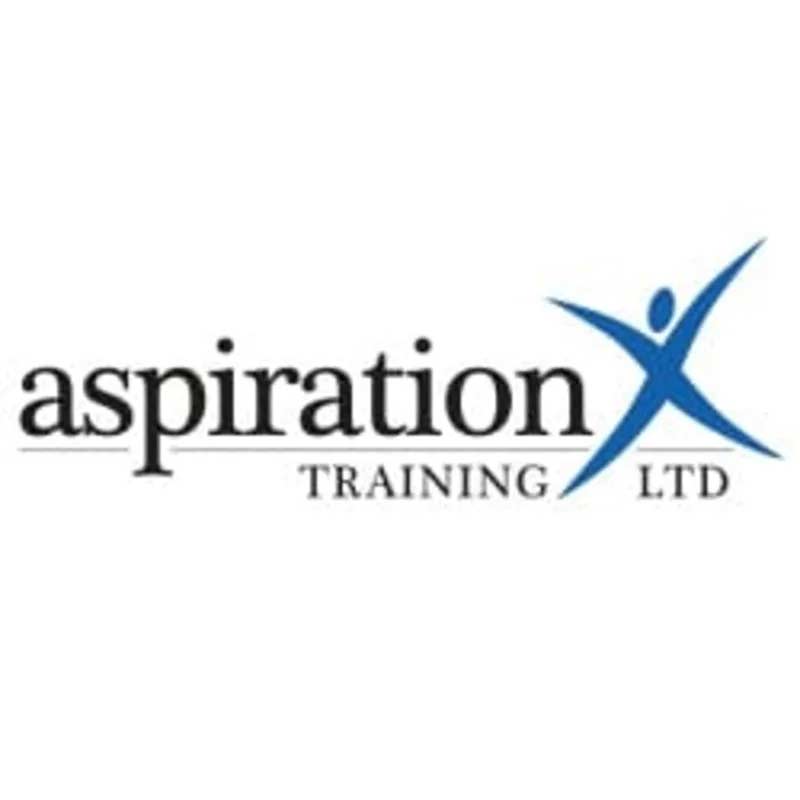
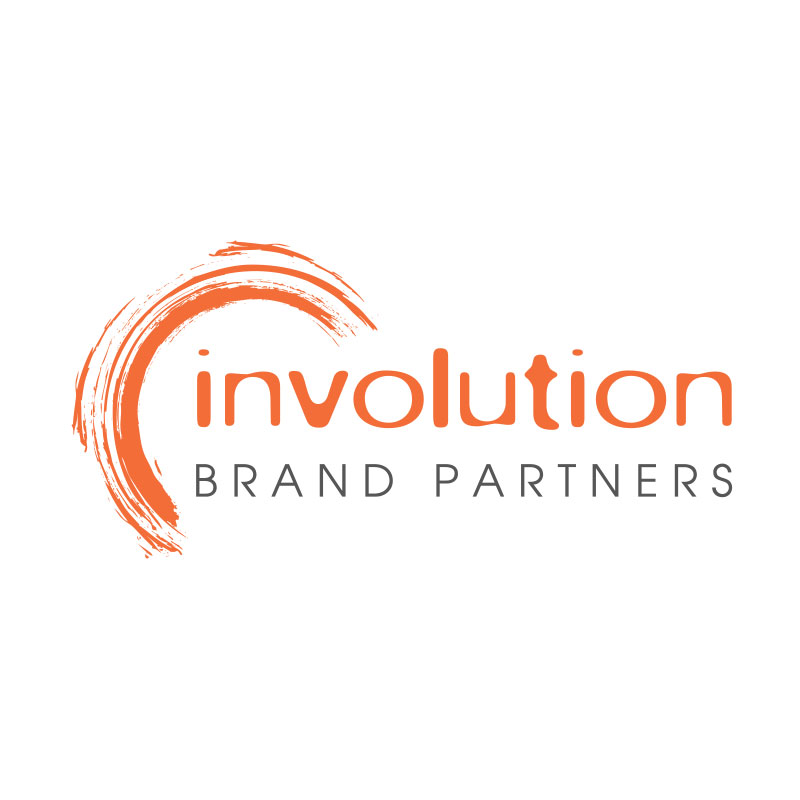
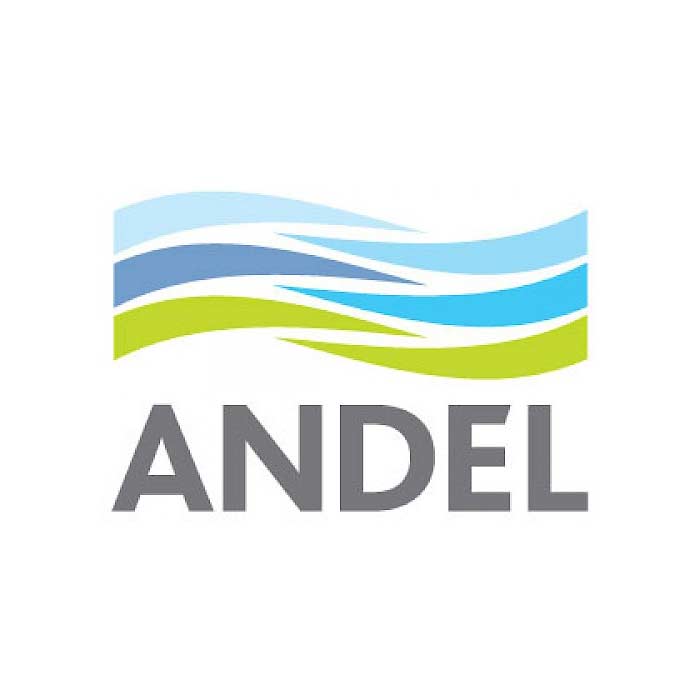
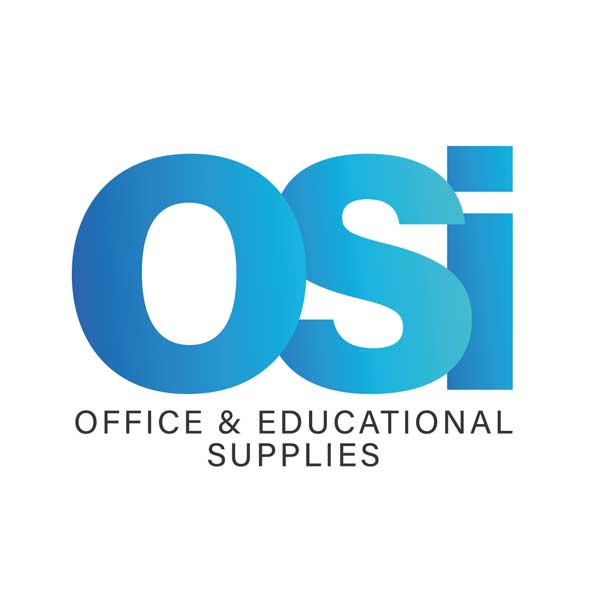
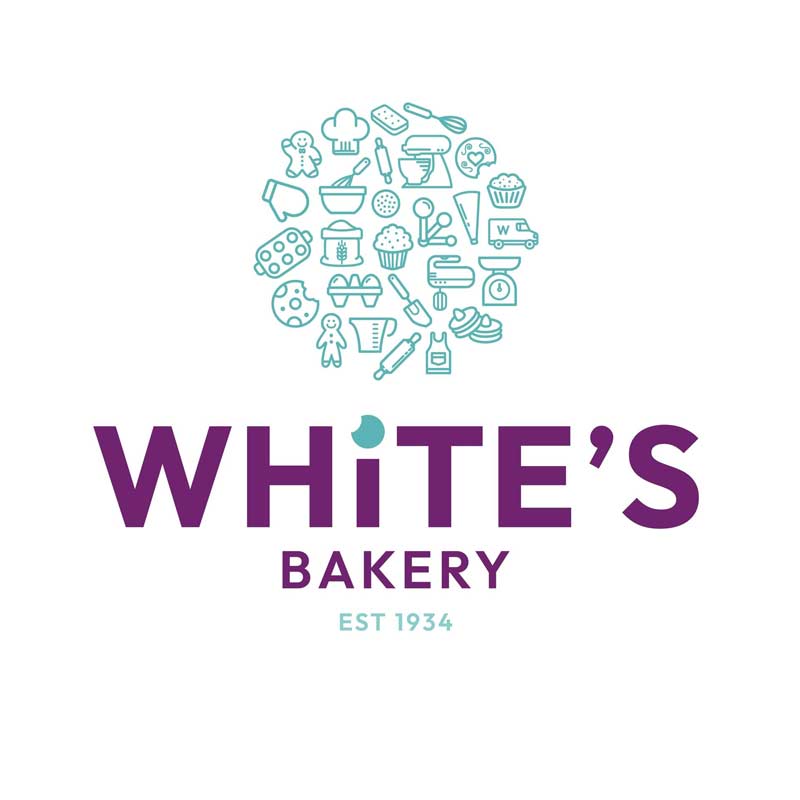
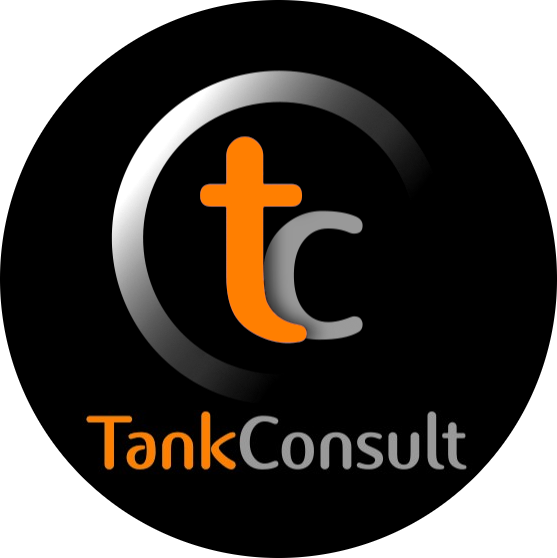
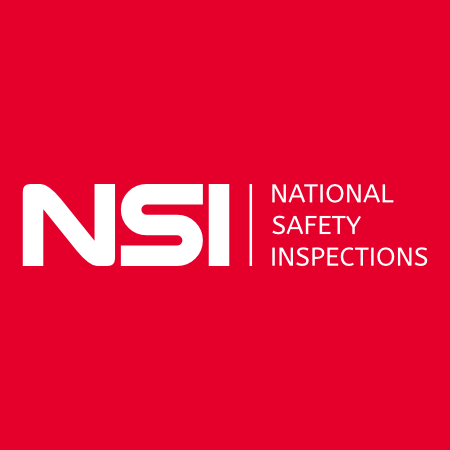
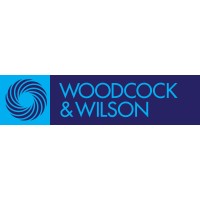
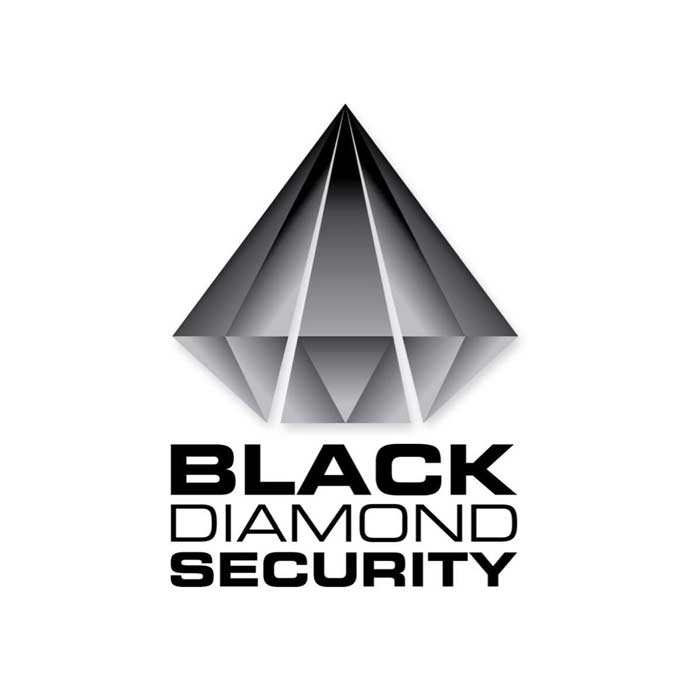
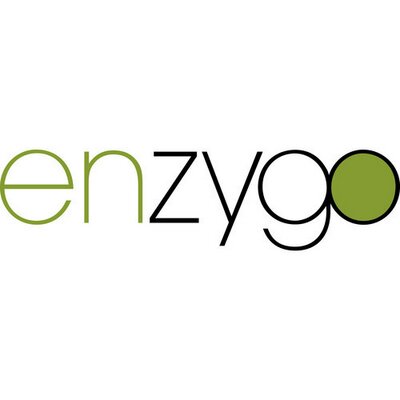